Features of Gear Cutting
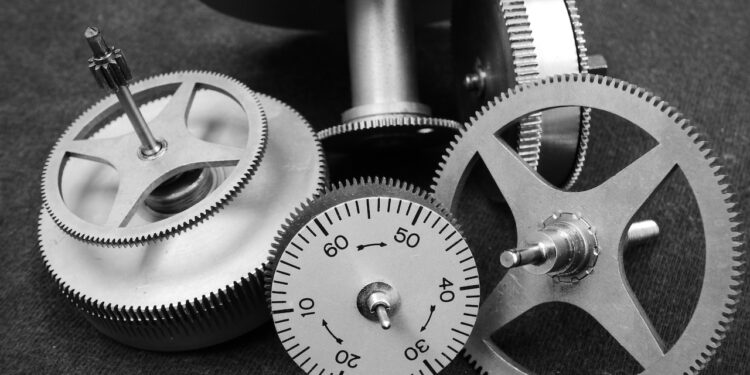
Developing intelligent tools and procedures is necessary for correctly manufacturing gears, which are crucial components of mechanical power transmission.
Gears are typically manufactured by casting, stamping, machining, and powder metallurgy methods. The most common and accurate machining processes for making gears are hobbing, broaching, milling, and grinding.
Table of Contents
Pitch
Pitch refers to the distance between two identical points on a gear tooth. The pitch of a gear is a critical factor in power transmission and has applications in many areas, including aircraft propellers, ships, and other industrial equipment.
Gear with a high pitch yields high speeds and efficiency, while a low pitch optimizes fuel economy and minimizes the risk of slipping in a drive. It is why many industrial sprockets are produced to this value and why the pitch of gear teeth must be consistent between mating gears.
Pitch is usually measured at a point on the pitch circle, and this value is also used to determine the number of teeth in a gear. It can be defined in three ways: diametral pitch (DP), circular pitch (CP), and module, also known as metric pitch.
Helix Angle
The helix angle of gear cutting Farmingdale NY is essential for any machining operation. It can improve the part finish, longer tool life, shorter cycle times, and more effective chip evacuation.
Helix angles might be between 12 degrees and 60 degrees. However, general-purpose end mills generally use between a 25 and 30deg helix angle where cutting-edge strength is maintained.
Higher helix angle end mills improve stock removal and reduce side loading. They also produce finer finishes.
A high helix angle also reduces the risk of deflection, which can lead to tool breakage.
The active profile of an involute tooth profile is the region between the start of the active profile (SAP) and the end of the active profile (EAP). Diameters or roll angles usually indicate SAP and EAP, with SAP being the lower value by convention.
Tooth Depth
The tooth size and naming ceremony of the gear-cutting world is undoubtedly the snobbiest part of the process. Hence, the teeth must be selected carefully from the bowels of a chuck and not just any old hunk of steel. However, the snobbiest part isn’t necessarily the worst part, and as long as the gear is free of oil and grease, it is quite a painless task. Fortunately, there is a foolproof method for ensuring that all the right shards are in place to ensure that all those sparkly teeth will be there for the taking. The requisite pre-selected shards are then glued into place to guarantee a smooth, stress-free cut. A subsequent swivel of the shards (if you can call it that) produces a finished gear that is both functional and aesthetic. Of course, the best part is that it’s all done without the aid of an overpriced lathe and without the need to buy a new miller or a radial arm grinder.
Material
In gear cutting, the material used for gears is essential. It must withstand high pressure, have good durability and endurance, and be malleable.
The material used for gears must also resist heat and oxidation. It is essential because gears are used in various types of machinery and equipment.
Typically, the material used in gear cutting is a metal or alloy. However, it can also be made of composite or other materials.
Some examples of the materials used for gears include steel, iron, and alloys. It is also possible to use other materials, such as titanium, niobium, and cobalt.
Another material used for gear cutting is carbide. It is a compound of iron and carbon characterized by its orthorhombic crystal structure. It contains 6.67 percent carbon and has a hardness of about 900 degrees F.